The Latest At Valley Forge
Reprint Courtesy of Mechanical Engineering Magazine
| by Edward Hayman |
Three little balls eliminate the need for a backup wrench during joint assembly.

As a thirty-year veteran of bolted flange joint assembly, I have witnessed many important improvements and also seen some gimmicks.
So I was skeptical when I heard about another washer, the Ball Lock Washer, advertised as eliminating the need for a ”backup wrench.” This is the second wrench needed when working a fastener that has a nut on each end. It holds one nut in place while the other is turned. The backup wrench usually pushes against another nut or the flange with the full force of the tightening torque. This often affords opportunity for trapping hands and serious injury. When tightening is complete, the wrench may have to be beaten with a very large hammer to free it from its locked position, creating another opportunity for injury. When loosening the bolt, the backup wrench can spin around and strike a hand.
I had seen other devices that were sup posed to eliminate the backup wrench, but they didn’t work well. They failed to consistently hold the nut stationary, damaged the flange face, caused increased post-tightening joint relaxation, or could not be used in conjunction with through-hardened steel washers.
The Ball Lock Washer is a washer that has three balls mounted in it. The balls are thicker than the washer and protrude slightly on each side of it. You place the washer between the nut and the flange or between the nut and a through-hardened steel washer [THSW). When the nut and Ball Lock Washer are forced against the flange during tightening, the balls embed into the flange or the THSW and keep the nut from turning. The company that developed the washer, Valley Forge & Bolt Mfg. Co. of Phoenix, has applied for a patent on the design.
I decided to perform some rudimentary tests to see if it worked. I chose several %-inch Ball Lock Washers.
Using an electric impact wrench and hand torque wrenches, I tried the washers with %-inch and 5/8-inch B7 studs on piping flanges.

At the end of seven hours, this simple device proved without failure to hold the opposite nut stationary under many different conditions with both slow and fast tightening methods. I t also held adequately during the initial loosening process. The balls in the washers completely embedded at about 25 percent of bolt yield which, in most cases, will result in no additional post tightening joint relaxation. The only damage to the fastener components or the flanges was three slight indentions. All tested washers were undamaged after repeated abusive uses.
Not having to deal with backup wrenches translates into quicker assembly, fewer injuries, and more efficient bolt loading. Using the Ball Lock Washers also allows for the application of lubricant on both ends of the stud and therefore more opportunities for ample bolt load application during assembly and decreased opportunity for galling or seizing during disassembly.
BP”s Cherry Point Refinery in Washington has developed special procedures that include the washers. According to Mike Marriott of BP: “We were exploring methods to reduce hand injuries associated with having to manually hold back-up tooling in place as studs were being torqued from the opposite side. Ball Lock Washers, in conjunction with Maly B lubricant, both helped to prevent hand injuries during this event and should minimize the occurrence of difficult breakout torque scenarios in the future.” I believe Mike will not be disappointed upon dis-assembly either.

EDWARD W. HAYMAN is a consultant in flange joint assembly, and is a member of the ASME Pressure Technology Post Construction Committee and the Subcommittee on Flange Joint Assembly.
By Bret Halley, Chief Operating Officer
The process of mating a bolt and nut together in tension has a long history, there have been plenty of changes in design and standardizations, but in tightening – most bolts still get torqued in some fashion. From centuries old wooden manufactured bolts and nuts hand fitted together, to modern day alloys made to many standards, most problems dealt with in the fastener applications are not developing or maintaining the design load in the torqueing process.
When analyzed, the manufacturing process controls, all the various bolting standards, material selection and design of equipment – the engineering level is detailed, documented and quite effective. Fastener installation however, relying on measurement of twisting force rather than equipment design load being achieved, does affect equipment reliability in our world today. Valley Forge has seen application after application improve with some form of design load verification. Application which have used our MaxBolt™ or SPC4™ Load Indicating fasteners, have data logged and enjoyed an added benefit of real time joint loading. Knowing what load is present in the fastener, or entire joint, no matter what tensioning system is used to install, increases product reliability, speed of installation and safety. Inspection of load rather than torque is attained in seconds with some load indicating systems. The International Fastener Institute (www.indfast.org) equates “nearly 95% of fastener failures are the result of poor fastener selection or improper installation”. With technology changing in the last couple of decades, torqueing or wondering if a fastener is loaded to design, is “old school” compared to engineered products on the market in the 21st century.
Valley Forge & Bolt’s history in supporting customers has driven us into ways we can inspect for load rather than just installing to a torque value. Not only do we think tightening fasteners to a verified load is the best way to solve problems for customers, we are building the future with being able to supply customers with ways to verify fasteners are correctly loaded. Our patent list is growing with specialty products, all centered on solutions to increase the odds of actually achieving and maintaining design load. The vision and goal of Valley Forge building load indicating fasteners, faster, better and cheaper is becoming a reality.
The Clarkester™ Tester for proving torque develops load in mill lining systems, is now a stocked item at Valley Forge with demand and results in the mining community. Information on load rather than torque is being discussed more often and products are readily available from Valley Forge and various other suppliers. ASTM F 2482 has laid the base rules for product classified as Load Indicating Externally Threaded Fasteners. As more sites and application benefit with the use of load for installation over torque, we push for engineered manufacturing to drive cost out and open the market to more than bolts labeled as critical in application. Predictive maintenance with the use of load in the fastener is being tested with instigating cracks in loaded fasteners. There is more to do and tests are underway with Wired and Wireless systems, temperature limits of reading bolts (currently reading at 640 F) and gauges. The future of fasteners is loaded, and we look forward to moving away from being torqued!
Hilton Head Island, South Carolina |
Michele Clarke had the arduous task of representing Valley Forge for the IFI Fall Meeting this past September. The Industrial Fastener Institute (IFI) is an institute that was started in 1931 to service the people, industry and customer of North American Fasteners. Valley Forge has been a member of this organization for many years. The venue was The Inn at Harbour Town on Hilton Head Island – with a PGA Tournament golf course available for the obligatory and very competitive IFI Golf Tournament.
The meetings are a chance for industry professionals to discuss many of the issues that are common to all of us. We were presented with the current economic outlook by Dr. Ken Mayland of ClearView Economics, Captain Ryan Davis, USMC, lecturing on what the U.S. Marine Corp of the future will look like, a presentation on McGill University and their engineering internship program, and Dan Sharkey of Brooks, Wilkins, Sharkey & Turco PLLC on contracts and litigation in the supply-chain. We also got updated on Government Issue by Jennifer Baker Reid of The Laurin Baker Group.
The next meeting will be Spring 2016 in Phoenix our hometown!
By Ron Clark, President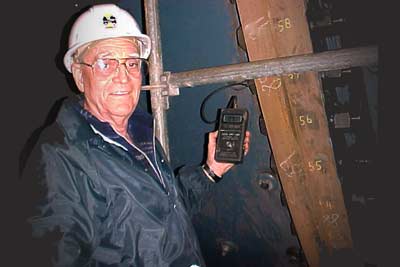
It is hard for me to admit, but alas true, that I was not always the all-knowing, wonderful, omnipotent,…. in bolting matters only of course… no purple cap here… ever modest guru, that all my three followers know me as. Feeling the need to help you innocent bolting engineers…. Halley to note… that are untouched by harsh reality, I swallow my pride to bring back that nightmare window from the past in this anecdote remembering the matter of:
THAT DAM VALVE.
Looking back I can see why it took months of trial and error to fix what I considered poor design causing a simple bolt breakage problem. The valve was a large poppit style, about a foot in diameter that was driven open to allow fast approach of the slide downward and closed, to transit into pressing speed, just above the part to be trimmed. The Press would run for a few days and crash. The 16mm bolt holding the valve in place would fail. Fast approach would not slow down to pressing speed and tools would say “ouch”.
After a few failures we decided the obvious fix would be to beef up to a larger fastener and then a larger yet when that didn’t work, and at that stage, we pick up the story which continues as everything in India does, at tea time of course. I spent more time drinking tea than working, so that’s probably why my eyeballs are still yellow… anyway, there I was, drinking tea and munching Samosa’s with my good friend Erik, the plant maintenance super, discussing the latest repeat event involving… right….. you guessed it, that dam valve on my #!@%$<> (adjective) German hydraulic trim press that had crashed again, and Alberts was there. Alberts was an older bugger, a nice enough soft spoken chap….. wasn’t even a mechanic because he was only a lowly electrical supervisor, and part of his job was replacing fuses for Pete’s sake. So naturally, following the industrial caste system prevalent at that time, was considered mentally inferior….. So of course I had every right to look down on him….
By this time everyone in the forge and his brother were aware of my valve problem and maybe the whole world for all I knew. My genius reputation caused by a swollen head was in danger. Listening to our frustrated conversation while drinking tea through a monster mug, Alberts, as others before him, mildly ventured a simple fix that he had used successfully on his bicycle pump, which brought laughs and jeers from the room, along with a rude comment by me as to where he could put the fix and the pump. Because most of my problems were with German machines I remember feeling in those early days that the whole German race was against me and that they were winning. Of course this could well have been because most of the machines I installed were German anyway and I was too proud to ask the engineers at Banning who I felt would laugh at such a simple problem! I was quite young but already showing my Guru qualities in stupid.
Fast forward six months and I am at Banning, the press builder, touring our German principals from whom the company I work for import and resell machinery. I unload all my pent up Valve misery including some under my breath on Herr Joachim, the unfortunate spokesperson from their engineering department who apologetically tells me that they do not use that system any more but that they had suggested a simple fix that had I possibly not received…. Call me sensitive, but I know he was slyly laughing at me. He then showed me a sketch of the fix, which left me red faced and many hat sizes smaller. It was Alberts’ bicycle fix exactly… even including leather as the material used to absorb the shock when the valve closed. Yes SHOCK, IMPACT causing load spikes were loosening and finally fatigue failing the fastener which did not require any assembly preload. But of course you all knew this and the moral of this story is less about bolting and more about listening. A little respect for other people’s opinions can lead to good things.
In conclusion… I heard that sigh of editor relief.
As your ever knowing…. etc. .etc.. modest as always, bolting Guru I would end by mentioning a tea party on my return from the Deutschland sponsored by me.. I paid… for Mister Alberts, no less, to acknowledge his successful contribution to the institute of unaware bolting fixes and other unmentionable things and to inform him that Herr Joachim would like to hire him as head of design fixes for Banning or was it banging… can’t remember but my head size did grow back to require extra-large Mexican sombreros…
OK the end.
Presentation at Maintenance Solutions Seminar
Indianapolis, IN
Held at the Westin Indianapolis and sponsored by the AIST Maintenance and Reliability Technical Committee, the 2015 AIST “Maintenance Solutions – A Practical Training Seminar” featured 28 events. Presented by industry leaders and subject matter experts, topics covered ‘Best-In-Class’ practices on Reliability, Hydraulics, Maintenance, Bearings, Lubrication, and Assembly of Bolted Joints.
Attended by 78 members of the Association of Iron and Steel Technology from the US and Canada, the guests were from a diverse background with a common interest in steel making.
Presenting for Valley Forge & Bolt, Jay Palmer educated and informed the “Bolting by Design” session attendees on the importance of assembly, as the often overlooked and frequently most critical aspect of insuring a reliable bolted joint. By covering the quality checks involved in all the steps of fastener design and manufacturing, it is quickly evident that conventional assembly processes have the least amount of controls with the fewest measurables, for proper tension when using methods like torque. Recognizing this common deficiency in assembly methods, the ASTM created F2482. F2482, the “Standard Specification for Load-Indicating Externally Threaded Fasteners”, takes bolt load to a higher level by creating a measurable quality standard for assembly that equals the manufacturing processes to make the bolts. To qualify for F2482, a fastener must provide a means to verify the desired clamp load upon installation and in service.
The group was very intrigued with load indicating technology as it uses elongation to precisely determine load. The need for accurate tensioning for safety and reliability is obvious and the attendees embraced the concept whole-heartedly. Numerous questions and positive feedback followed, accompanied by heads nodding in agreement. Follow-up ‘lunch and learn’ presentations are being scheduled for maintenance crews at mills.
To learn more or to get your copy of the presentation click here.
The Good, The Bad and The Ugly!
At the great Victoria in London, Barry Thomas presented “The Good, The Bad and The Ugly” to the London Forum of the Heat Transfer Society on September 17th, 2015. Barry talked about bolted joints and explained the advantages of Load Indicating Technology. He has wide experience in bolting technology going back to 1972, including specific experience in the oil and gas industry and applications in structures, mechanical equipment, cranes and pressure vessels. If you happen to be in London make sure to stop by!!