The Latest At Valley Forge
Our newly installed “Heat Treat” department has settled into full production mode. Forecasted production schedules are being predictively met. To insure continuous throughput, operator training is now underway. We have incorporated Metal Training Institute (MTI) for our heat treat training program. We have implemented Class 100: Qualified Furnace Operator and Class 150: Heat Treat Technical Specialist (HTTC), as standard practice for our operator training. Under the supervision of Randy Stotts, we continue providing our customers with the highest of quality products while meeting their scheduling needs.
by Glenn Snowberger
ASTM International is an organization that develops and publishes consensus technical standards for 12,000 plus materials, products, systems and services. Within the many technical committees there is a specific section devoted to fasteners called the F16 Committee on Fasteners. Valley Forge has been a contributing and voting member of ASTM since 2000.
When you see a fastener with a grade identification marking, such as “BC” or “BD”, have you ever thought about what it refers to? These markings signify that the fastener has been manufactured and complies with a specific technical standard, in this case ASTM A354.
In 2002, Valley Forge recognized the importance of having a consensus standard detailing the requirements for Load Indicating Fasteners (LIFs), both the MAXBOLT™ and SPC4™. We then approached the ASTM subcommittee, F16-02, for steel bolts, nuts, rivets and washers, with a proposal to develop this standard. After discussion within the committee it was determined that a Work Task Group would be formed to develop the standard. After two (2) years and several ballots, a standard was presented to F16 for acceptance which resulted in the publication of ASTM F2482, Standard Specification for Load-Indicating Externally Threaded Fasteners.
With the publication of the standard, several companies have approached F16-02, proposing that their product be included in the specification. In the case of RotoBolt®, following discussion and comments over several committee meetings, it was determined that a Work Task Group be formed to develop a new standard. The rationale for this was that the product was an attribute (Go/No Go) type of system not offering a true measurement of bolt tension. This product informs the user, through a “finger test” method, that design tension has been reached. Subsequently, a Work Task Group was formed and work began on the standard, however, after a period of time the work was abandoned. RotoBolt® withdrew from the effort, resulting in the Work Task Group being disbanded and the Work Item Number being closed.
In 2013 the F16-02 subcommittee was approached by Stress Indicators, Inc. to ask for the opportunity to have their SmartBolt® fasteners included in ASTM F2482 standard. A presentation followed that detailed the product and how it enables the user to determine that the proper bolt tension has been achieved.
The discussions that followed centered on the question of, “Does the product measure bolt tension?” SmartBolt® was promoting the idea that the change in color is a measuring tool. There were many opinions that this product was also an attribute (Go/No Go) type of system, since the product provided a visual indication of tension being achieved. There was however a decision by the committee to assign a Work Item number and form a Work Task Group so as to move towards possible inclusion in F2482. This represented a major change in direction by F16-02, which we will explain later.
Work on the proposed changes or additions to the standard were completed and the proposal was submitted for a ballot which closed on January 20, 2014. At the May 2014 F16-02 meeting, the ballot results were presented with the negative votes being found to be persuasive. This then required that the ballot be revised or amended and then re-balloted. At the November 2014 subcommittee meeting, Stress Indicators, Inc. expressed their continuing interest in pursuing inclusion of their product in the standard. At the May 2015 meeting it was announced that the SmartBolt® work item had been withdrawn and was no longer on a ballot.
Now as Paul Harvey said here is “the rest of the story”. You have to wonder why F16-02 would move ahead to consider inclusion of an attribute type product into a standard that clearly specifies measuring capabilities? ASTM F16 has looked at and determined that due to the large number of standards that are in publication, many of which are similar, they would attempt to combine standards wherever possible when they are subject to review. This is similar to the earlier movement to have inch and metric products covered in one (1) standard. This direction will clearly be shown with the publication of ASTM F3125 Specification for High Strength Structural Bolts, Steel and Alloy Steel in 2016. This is the inclusion in one (1) specification of ASTM A325/A325M and ASTM A490/A490M.
Because of the directional change by ASTM toward reducing and combining standards it is possible that in the future an attribute (Go/No Go) type of system for indicating fastener tension will be included in the ASTM F2482 specification. Valley Forge will continue to work to see that if this does come to be, the standard will have clear and precise distinctions showing the two (2) types of products. We will clearly advocate for the total separation within the standard so as to protect against anyone concluding that the two (2) types of products are the same and therefore equal, which they are not.
By Ron Clark, President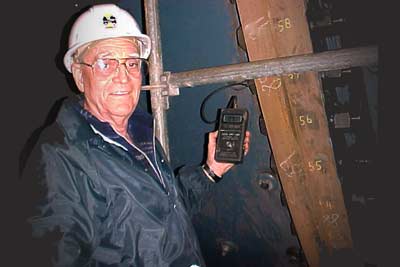
Prologue
Decapitated little fasteners are never a pleasant recollection, so to my publisher, may you be buried under an avalanche of ISIS propaganda for persuading me to recall this traumatic event —— moving on—- so did you know publisher, that just like books, anecdotes should have titles. However, unlike books, it is possible for a reluctant author like myself, to craft a title with such literary skill, that after writing said title, no more words would be needed for the rest of the anecdote. With this stationery saving plan in mind, I have struggled to title the event I am about to describe, in the hopes that a single line would be large enough to satisfy your picky professional standards—– but alas, literary success eludes me once more. So to my multitude of readers —- I tried —– what’s that I hear —– long winded—– It’s the publisher’s fault.
Guess this title!
I’m not going to reveal them yet, but even though I failed to use them I did come up with a couple of titles of my own. The one is from a poem by Kipling, and though the line is taken out of context and certainly not applicable in this century, it could well have qualified for the event in the year it happened. Of course the other title had to be words in a song. Both poem and song were well known in an age that may unfortunately disqualify many readers in our jointing world, but alas, with historical precedent on my side, I am left with the sad decision to not glue, but screw, equal opportunity.
Background Info
The place was Jamshedpur, India in the early sixties, where, even though living in Calcutta, I spent months of my life installing and servicing American, German and Swiss machinery at TATA’s Daimler Benz auto forge facility. Welcome a participant into the story, a maintenance mechanic at the plant, a character named Charan Singh, whose “man bites dog” attitude was known and generally tolerated by fellow workers and supervisors alike, and of course known to me, an outside contractor who had achieved the impossible by successfully working with him over the years. Other than a passing hand wave, I had not been officially introduced to Gruber the unwitting ‘other’ participant of this narrative, whose first name was Peter. Gruber had recently arrived from Germany to work on a very large, ailing, double acting hammer. Peter had no English so could only communicate with hand signals and guttural utterings which no one understood.
It was thought that the cause of their mutual dislike probably started early on when Peter in a combined flash of inspiration—desperation, had attempted to communicate with Charan Singh by drawing pictures on a pad, but the point of his lead pencil broke while negotiating the left arm of the swastika, bringing a rude snigger from Charan— sending said Peter into an awful Teutonic tizzy—worsened, when no one could find him a pencil sharpener. Perhaps this portended—is this a word Publisher?—events to come, and not long after, it was Peter who decided to stop me with a Tarzan like introduction wearing a huge cheeseburger smile, by sticking his ham of a hand on his considerable chest and saying ‘Me Peter’.
Seems like Peter had a suspicion that since I worked on German machines I was a kindred spirit and the answer to his communication problem, with his upcoming hammer rebuild. Had I known what lay ahead I may have caught the first plane back to Calcutta, but looking back, I now realize I was witness to the birth of the expression “Getting Torqued”.
The Players Bio
Peter Gruber was a large, genial, beer drinking man with a red face and hams for hands. Peter was not just a mechanic—he was a “German mechanic” and despite communication difficulties, managed to constantly convey his undeniably superior qualification to Charan Singh and crew with unmistakable intent.
Charan Singh was tall, wiry, middle aged and turbaned, a very proud Sikh—- who was a self-taught mechanic, as many were in India in those days. Fully self-reliant and ready to take on any challenges, he had worked very well with me on large press installations over the years. Acknowledging what one
doesn’t know can make average people successful. A little knowledge is sometimes dangerous and Charan would never admit to a mistake because his pride would not let him. As a result he was often involved in sometimes near violent altercations with colleagues and higher muckimucs.
And then there was I, the innocent peacemaker in this impending incident. I got on with most everybody because early in my life I realized that no matter how smart you think you are there is always someone around the corner who is smarter, and who you could learn from. But even I, with my self-admitted diplomatic skills, failed to heed the warning signs.
The Incident or “Death of a Diaphragm”
It was Charan Singh who drug me away from my afternoon tea at the maintenance manager’s office, to be present while he and Peter assembled the critical hammer diaphragm. The circular diaphragm was about five feet in diameter and was bolted down with a series of what looked like 5/16” hex head screws. The assembly sat on a workhorse and had been prepped by Gruber with German precision, with all screws snugged down, sequence marked and ready for the final tightening.
The plan was for Peter and Charan Singh, both experienced wrench turners, to sit on opposite sides while torquing the screws simultaneously in a sequence recommended by the manufacturer. Things went sour from the start when Charan Singh accused Peter of sitting on the wrong side of this symmetrical assembly. When the smoke cleared and order restored, it turned out that the side had nothing to do with it but that Peter was sitting on Charan Singh’s favorite stool. I was beginning to think that there must be some truth in the rumor that Charan Singh went nuts after twelve o’clock. So sides were switched and order restored by my diplomatic self, or so thought I.
I would inform some of you— dare I breach PC again— younger readers, that in the days before “click” torque wrenches, accurate preload on small screws was totally dependent on the mechanics skill. So the job ahead for the two proud mechanics, one from the east and the other from the west, demanded considerable skills. So there they sat on their stools like two pugilists waiting for the bell. Would have been a great iPhone moment.
Peter made the first turn on position marked # 1 with Charan simultaneously covering and torqueing his #1 on cue… The sequencer, seated on his own stool, lifted placard #2, so both mechanics covered #2 and torqued on cue. #3 was completed smoothly and I thought maybe this is working. #4 went fine and I called a pause after #6 to reorganize the placards. We restarted at #7 and after cue was called at #8 Charan Singh’s ring spanner came away with a head still in it and all hell broke loose. The German mechanic uttered a shrill scream of anguish and anger, the sequencer fell off his stool and I could have sworn that the wounded diaphragm resonated in tune with Peter Gruber’s vocal misery.
What happens next would have caused an international incident if anybody could have found us on the map. Gruber, yes the same Peter Gruber, covers #9 and with a casual snap of his wrist and to the surprise of all, willfully torques the head off. Rightly sensing a slight and not to be outdone, Charan Singh quickly responds by torquing off the heads of both his #9 and #10 in quick succession. All this happens at warp speed so that when the dazed sequencer props himself up with the help of placard #10, Gruber obliges by decapitating said screw with a flourish. After all befell ist befell, ya!
Like watching a tennis match all eyes turn to Charan Singh in anticipation who promptly removes the heads of his #11, #12 and #13 and stares at Gruber with a challenging glare that almost says I can do anything better than you… It is at that precise moment and in pin drop silence, when Gruber’s wrench is poised and ready to retaliate, that the calm, cautioning, changing voice of the maintenance manager is heard saying, “Be careful you buggers, don’t shear off any heads, we don’t have any more special screws —— daaaamn.” And sanity returns as all faces turn to my good friend Eric whose last name I shall withhold because he has either passed on or is still in hiding.
Epilogue
Had there been an international incident resulting from Gruber’s behavior it may have brought forth press like this:
India government lodges complaint with FRG embassy in New Delhi over events involving destruction of property by FRG passport holder and fugitive Peter Gruber last seen fleeing the scene with bearded Sikh in hot pursuit.
India PM in heated talks with German chancellor who finds Gruber’s behavior unacceptable—- now I know where Obama found that word. Chancellor makes light and challenges PM to a beer drinking contest.
PM declines indignantly—- he only drinks Mango juice but since he is the offended party he has choice of weapons and chooses instead a hot chili eating duel. The chancellor accepts, while citing precedent, volunteers his vice, who is Mexican, to be his champion. PM is snared in his own trap when his own vice unexpectedly pleads a sudden case of hemorrhoids.
Indo-German relations restored.
Not so well known diplomat also known as Mr. Bolt restores Indo-German relations by eating the Indian chilies and drinking all the German beer.
Mercifully— The End.
As Published in the April 2015 Issue of Wind Systems
| By Rusty Flocken |
In fastening, joint tightness is nearly always associated with the use of a calibrated torque wrench during installation. However, for any given fastener, the relationship between applied torque and resulting tension is anything but direct. This is no fault of the torque tool, but simply a short- coming of the method itself; installation torque is not a measure of joint tension, it is purely a measurement of applied tightening effort. The primary reason for this is the influence of friction. When a fastener is tightened to a prescribed torque, this value has been calculated using a targeted clamp load and a nut (friction) factor. Variations of up to +/- 30% can arise at random with multiple fasteners from the same lot developing varying amounts of friction due to natural surface imperfections. Even within specification limits, variances in hardness and/or material properties can also impact accuracy.
These same errors within the torque-tension relationship also exist when verifying or maintaining bolt tightness. In addition, the process takes a lot of time and may result in little to no gain in joint integrity. As an example, say your coffee cup has been sitting for some time after being filled and you don’t want to drink cold coffee. You do not check the temperature first, but rather, you warm it in the microwave for 30 seconds. Without first checking the temperature how do we know if the coffee will be too hot, or just right? Perhaps it did not need to be heated at all. This may sound elementary, and yet it is exactly what we are doing when we check a joint for tightness with a torque wrench: the tightening process is repeated to ensure that the same tension achieved at installation is maintained. Is the time spent re-tightening actually doing something useful? Using this re-torque method, do we really know if a bolt is loose? Rather we assume they all could be loose and tighten indiscrim- inately. However, there are means to verify tension in a bolt without put- ting a wrench on it.
Available methods for measuring bolt tension during and after installations include length measurement, direct tension indicators, and load-indicating fasteners. Of the three methods, load-indicating fasteners (LIFs) have proven to be the most beneficial for a number of reasons. LIFs are capable of showing real-time fastener load up to the material yield strength continuously throughout the life of the fastener. With a LIF, accurate and fast load readings are possible without special operator training or the need for keeping records or calculations to determine tightness. To verify load, an operator does not require any bolting experience, as this information is read directly from the fastener. The use of a detachable load-reading device may be required. Additional benefits can include automatic torque tool control and bolt load data logging capability. This means that bolted joints can be tightened and maintained more accurately, quickly, and with data to support that they are safe and properly loaded.
In fastening applications where joint tension is controlled, the only direct means to do so is with a LIF. All of the drawbacks of torque and tension tightening methods are no longer issues when standard fasteners are converted to, or replaced by, LIFs. With load indicating technology, every bolt is a calibrated instrument. More focus can be placed on achieving and maintaining proper bolt tension and less focus on procuring the tools and experience traditionally required for this task. This means a quicker, safer and more accurate wind power installation, more effective maintenance, and a longer life span. Also, newly developed technology for multiple bolt reading capabilities, for wind turbine applications, in both wired and wireless forms, are available. Numerous other industries have approved the use of LIFs to satisfy warranty and insurance requirements. Now there can be savings in time, labor, and other expenses in tower bolts, by using LIFs to satisfy the mandated inspection of the bolted joint.
For over 15 years, Valley Forge & Bolt Mfg. Co. in Phoenix, Arizona has dedicated extensive research and production to these innovative, patented fasteners and are the only manufacturer worldwide.
VFB Interview With Brad Webb of AC Sailing SF
“It all started when Bengt Blenduf, the well-known, international bolting Guru and educator was approached for his design recommendations by the Oracle/BMW racing team for their keel bolts. He thought it would be a great application for our load indicating technology, so he called me and directed me to their engineering. Valley Forge designed the hardware for the Maxbolt™ with the Oracle engineers, as you see it today.”
– Ron Clarke
VFB: How long you have been racing boats Brad?
BW: I started sailing when I was 12, in just a little dingy, in Wellington, NZ. I used to enjoy sailing on my own but for whatever reason, I enjoyed sailing with other people more and as I got further into it, I realized as much as I was quite a good driver, a Helmsman, I was a better crewmember, especially on the bow at the front of the boat. And then, my career happened more by accident then by good management. I decided to take a couple years off just to figure out what I wanted to do with my life: that was 20 years ago. I grew up looking at the big glossy magazines, with nice boats and sun drenched ports, and that seemed to me like a pretty good way to spend a couple of years. I wanted to go and sail the big blue water events, I wanted to sail on big fast boats, so I did. I had this drive to be better, I wanted to do things better every day I went out. I started sailing on the match racing circuits around the world, with some different skippers and my first America’s Cup was in 1995 in San Diego. Again it was more by accident than good management. Between 1995 and 2000, which was the next American’s Cup in New Zealand, I went sailing around the world, and sailed in a lot of different places. I think there was 140 events in 16 different countries over four and a half years. I did a lot of sailing, and sailed with a lot of people, in a lot of different situations and gained a lot of experience. When my second America’s Cup came around in 2000 with America True, the San Francisco team, I was pretty well prepared. Later that year I was picked up by Oracle Racing for the 2003 America’s cup, and I’ve been with Oracle Racing ever since, 5 campaigns and over 14 years.
VFB: Tell us about USA 76, the boat that has Valley Forge Maxbolts™ in the keel?
BW: I sailed in the International America’s Cup Class (IACC) for four America’s Cups, from 1992 to 2007. That is what USA 76 is. The IACC, and the USA 76, was a great, great class, for 15 years, they built 100 boats. They are all sequential, so USA 76 is the 76th boat built. We were never successful winning the Cup in that class, but they were just a great boat to sail. We sailed with 17 people on those. Everyone had very, very specific roles, and the choreography that needed to happen on board to get the boat around the course, changing sails and sail it well, was quite detailed. If you got it right, you could have a great day out. And if you got it wrong, it was a bad day. The boats were very fast. We would sail around in those boats at 10 to 15 knots. Then we transitioned into the big T Hulls, and now we have transitioned into foiling catamarans, which are now sailing around at 45 knots. Quite a big jump in just a few years! But I bought USA 76 because I thought San Francisco needed some kind of connection to the America’s Cup. It’s a great boat, I know it well, and we put it together here in 2011, and we have been running it as a charter business out of Pier 39, coming up on 4 years now.
VFB: What distances did USA 76 race?
BW: We used to sail the IACC on a course that was effectively 12 miles, although you cover a lot more distance when you’re zigzagging up. Those races were about an hour to an hour and half long. We are now doing the same distance for the last America’s Cup in 2013, in San Francisco, doing the same distance in about 25 minutes in the catamarans. Still kind of doing the same distance but screaming around the race course.
VFB: What about the conditions of the race? What variation is there that the boats sail in?
BW: It really depends on the venue. The America’s Cup was held for a long, long time in Newport, Rhode Island, which was fairly benign. It would be 10-15 knots and fairly flat water, but quite consistent. When Australia won in 1983, they broke the longest winning streak in history and took the event down to Perth. The Regatta was held offshore there, and it was extremely windy with big waves. For those who watched, like me as a kid, it was extremely exciting because it was wet ‘n wild with thrills and spills. Then it was won again by the American’s and taken to San Diego which is inherently light, so the yachting there wasn’t all that exciting. New Zealand won it in 1995 and took it to New Zealand. That really showed what sort of range these boats can go through. We would have very light winds or very heavy, in fact in 2000 it was extremely windy. But again, you can have days that were light and then days that were wet ‘n wild and great TV viewing. They generally stop racing the boats at about 30 knots of true wind. For a couple of reasons, safety primarily, but after that, it’s tough to even watch and it’s even tougher for the race committee to set a fair course. At that point, it gets pretty extreme, boats are dragging anchors and it gets a little brutal. But that has generally been the range, from about 7 to 27 knots, so there is a significant amount of variation in the sailing conditions.
VFB: How much are the boats sailing? In terms of the years that the Maxbolts™ have been in the keel?
BW: For the IACC [USA 76 class] we used to do a lot of sailing, we would set up at a venue, or different venues around the world and do a lot of sailing. Once you had them together, they were an easy boat to put in the water and go sailing. The catamarans are logistically a little bit harder, because you have to put the wing and platform in everyday, and you have to use a crane. Just logistically they are a lot tougher. The cut boats we used to sail a lot, especially when we were based in Valencia. We sailed probably every other day for three years. That was a lot of sailing. Then, when we weren’t sailing, we were off sailing some other boats. So the USA 76 has been all over the world sailing far and wide; Auckland, Australia, all around Europe, lots of sailing in Europe, and both coasts of the USA.
VFB: How was USA 76 designed?
BW: It’s generally started using CSD analysis and making a hull shape, that is as fast as it can be built. And then the next part is engineering a structure that is as light, but as strong as it can be built. That then becomes part of the keel equation. But then you have to build everything else around it; the sails and the systems on board. Again, the lighter that you can make everything in the hull, and everything above the wood line, the more lead you could put in the bulb, because it was an overall weight that was part of the rule. Which basically makes the boat more powerful, which made the boat faster. If you could make the boat more powerful, it basically meant you were putting more lead in the bulb, but it then also meant that your keel, keel structure and all your fastenings needed to be engineered to take all that extra load. It’s a very complicated puzzle that needs to be just about perfect to work. There’s no room for error.
VFB: Where there bolting issues being encountered when you first came to Valley Forge for fasteners?
BW: There wasn’t necessarily a bolting issue, the Maxbolts where just the right product and application because you can see what the loading was. You can see that you were getting the numbers that the designers were asking for. We rely HEAVILY on analytics and engineering and design numbers, not only to build it, but to maintain it and monitor the boat, day in and day out. [When racing] we would take the keel on and off of this boat, probably once a month just to check it and make sure nothing was going wrong. For me it’s just all about reliability. Reliability was a HUGE thing for us when we were racing this boat because we had to finish races. We have to have faith in our gear. My mentality now is on a commercial operation, inspected by the coast guard, and I have paying passengers onboard. My liability is huge. Keels have fallen off and broken off America’s Cup boats in the past. Generally not because of the bolts, but for other reasons through fatigue and poor engineering. That still doesn’t mean that I want to risk sitting back and not doing anything. I have a lot of faith in how this keel was engineered. On these boats, the keel is just a huge, huge deal. If you engineered the hull and the rig and everything else light, there was more lead you could put downstairs. But it also meant the keel bolts were going to be working a lot harder, so the keel bolts were a huge part of the equation when these boats were being built, the way they’re engineered and the way the whole structure was engineered around the keel. Everything else doesn’t see that kind of load. I am quite close to the guy that designed the keel in the first place. We constantly talk about cycles and fatigue that the boat is going through. We took a lot of lead out of the bulb when we put it back in the water [commercially] and took some sailing rear off. So the bolts aren’t under what they were designed for, they aren’t seeing the design load they originally engineered for. It would be quite a lot lower. However, they are seeing a lot more cycles than they were originally engineered for. Which is why we haven’t had a lot of concern, because we think there have been some tradeoffs. Now that it’s been four years, we think the prudent thing is to take them out, check them, have them tested, put new ones in and see where we stand and ensure that we have confidence in the boat forward.
VF: Tell us more about the Maxbolts™ in USA 76?
BW: The first set, they used to go in and out every month. That was when we were racing. Since I have bought the boat, and have a commercial license, we put a new set of bolts in the boat in 2011 and haven’t touched them since. We originally put them up to about 80% of their max loading, which we were happy with, and they haven’t moved. We have made sure that we have kept them nice and greased because they are in a pretty harsh environment, so we try to look after them as best we can. Now we are taking them out and putting a brand new set in. We are going to send them back to Valley Forge for testing and that will give us an accurate picture of life and the environment that these bolts have been in. What we are going to learn when the new bolts come and we swap them out, is if there has been any fatigue on them, or excessive amounts of corrosion, just what’s going on. For a number of things, but mainly we can learn what kind of long term environment they can go into. For us, it gives us an idea of where we are in the cycle of these bolts. When we put these brand new ones in and send the other back and we find that they are absolutely pristine, then we know the least amount of time we can get out of them, without any concerns.
Post interview update: The USA 76 was taken out of the water on March 18th at the KKMI Marine Facility in Port Richmond, a first class boat yard in San Francisco and AC Sailing’s first choice for haul out and maintenance needs. They removed the in service Maxbolts™, and installed the brand new set. The photos show her out of the water with her 14 foot long keel and 40,000 pounds of lead attached at the bottom. You can see the installation using the VF hydraulic wrench and the new bolts in position and tensioned. The bolts were fully lubricated, then painted with an epoxy protective coating after install.
By Ron Clark, President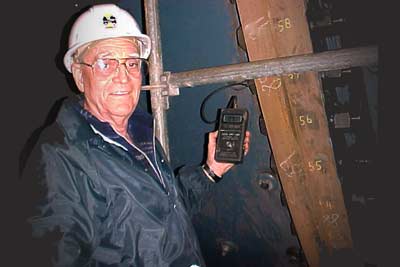
I don’t know if our editor will print this. But she’s Canadian….
‘OSHA’ AHOY. Where were you when I never heard of you, and after I heard I wish I hadn’t?
Firsts of anything tend to stay in our memory forever. So let me bore you with an anecdote of mine. Way back in my misspent youth I ran away from my apprenticeship at India’s largest steam locomotive workshop in Jamalpur to join the ‘boats’. Boats was a word used by us apprentices to widely mean the then, merchant navy. Word was out that steam engineers were needed, adventure called and I answered with all the unspoiled naivety of a teenage idiot.
Calcutta was the port, the SS DUMOSA was the ship, and I was signed on as the extra 5th engineer. Old man Punchard who hired this skinny looking runt, must have been seeing double during our interview, but I prefer to think he foresaw the makings of a great engineer happening before his bleary eyes.
Young Sailor RonThe DUMOSA was an Aussie Tub with significant similarities to the ARK. It floated and was close to the same age. It had been bought by a group of Boorie’s and had “cargoed” (is that a word?), to Calcutta and if it survived the voyage, it was to proceed light ship to the port of Karachi, in the newly formed nation of Pakistan, to be broken up for scrap. Nobody told me about all this or that most of the crew had deserted at Calcutta when I signed the articles. Maybe Punchard was not so drunk after all. Looking back I think there must have been many no takers, who were better informed.
First working day loomed and it fell to me, the extra 5th to supervise the lascars unloading cargo at the lone steam winch on deck. I knew winches lifted things and I’d seen them on Hollywood, ship movies and stuff, but had never worked anywhere near one before. Undaunted by my supreme ignorance and with steam snorting and leaking everywhere, things went fine until they didn’t, and the dam winch went nuts. A shackle pin fell out of a lifting clevis and a bundle of something came apart and hit the deck from what seemed the height of Mount Everest. To put the chaos that ensued in nautical terms, after all I was a sailor now, buggers were running to port, starboard and all points of the compass to escape the rain of errant cargo with me in the vanguard. I make no apologies but at that tender age, self-preservation and visions of life after the winch came to the fore, and aren’t you glad I survived to tell the tale. Notwithstanding my winch crews best efforts to the contrary, there were no casualties, though is those days, who the hell was counting. Lots of glowering and not so nice comments for the winch crew even though we protested our part in the incident as being just collateral damage. I didn’t know it then, but I think we might have invented the phrase collateral damage that is so glibly thrown around by politicians today.
Somebody important, turned out to be a cabin boy, suggested the captain be informed of all disasters and other things. Someone else reminded him that, there was no captain. Seems like Captain Bratton, jolly old tar that he was, had sailed his last voyage on the SS DUMOSA. Passing into the ghost ocean a few days previous and a new captain was on his way. Also seems like the unfortunate chap lay dead in his cabin for awhile before being noticed and like all jolly captains had to be winched off the boat after great difficulty in getting his great size out the cabin door. I got this information on good authority and with great detail, because cabin boys know everything.
What has this got to do with bolting you say? And I say I’m getting to it, so give me a break. After sixty five years I think I’m still traumatized by almost being collateral damage at the incident of the winch.
I hadn’t met the Chief Engineer yet. My source, yup, the cabin boy informed me that his name was Reynolds, and that he was so old that he looked like he’d escaped before the embalming was completed. He also confided that he was irreverently called Rundu, behind his back when not politely addressed as Chief. The 3rd engineer arranges the day to day operation in the engine room and it was Ghose, a Bengali engineer, who finally appeared on the scene.
With all the bright minds around it wasn’t long to diagnose stripped threads with the nut falling of the end of the shackle pin. Of course, at that time, I didn’t know a shackle pin from the Queen Mary but I did recognize the problem with the threads. (Unknown to me I was already fulfilling Punchard’s bleary vision of greatness).
When it was discovered that there were no shackle spares on board and no way to procure the hardware without idling the winch for hours, Ghose, who was also newly signed, went ballistic, muttering all kinds of disbelief in Bengali, which is a very suitable language to express frustrations and can be easily mistaken for French after a few drinks. Somebody found the nut, no it wasn’t the cabin boy, but the ANSI standards committee would have had significant problems classifying the fit or lack thereof.
Enter Chief Reynolds. He had shuffled alongside unnoticed. One look at him confirmed the suspicions of the cabin boy. I later heard that he was an old man even before 1941 when he was sailing with Atlantic convoys in oil tankers. There were not many engineers with the courage to stay below in oil tanker engine rooms on U boat waters. Evidently Reynolds was one of them, a survivor and a legend in his time, but now a wizened up shaky old relic of the past, who wouldn’t leave the sea. Or so I thought in my young wisdom.
Ghose explains the situation to Reynolds who peers at the hardware using a magnifying glass. Ghose leaves but returns with a steel shim and a pair of tin snips. Reynolds surprises me by skillfully cutting and shaping a strip off the shim and then inserting it into the nut. Ghose then threads on the nut and, Voila! The remaining threads develop enough torque to permit the shackle to operate safely for a few hours. We cautiously begin unloading again. My crew are winching again but lascars maintain a safe distance.
So I put it to you my readers, if any, as a popular though never published author, was this my first bolting lesson or a larger one where the ends justifies the means or, always find a cabin boy for information because they know more than the NSA.
My shaving mirror frightens me every m orning because I’m starting to resemble Reynolds. But the final lesson for y’all out there is, never judge a book by its cover, because maybe, just maybe, Punchard was right.
For more on my voyage to Karachi check in on the next newsletter if Lana agrees to go to print, that is.