Industrial Machining, before the turn of the century, was purely used to refer to anyone who worked on “machines”. In that capacity, those who referred to themselves as “machinists”, were simply those who built or mended machines. In the years prior to 1945, the Machine Age, machining referred to the more “traditional”, and often done by hand, processes, such as turning, boring, drilling, milling, and shaping. Towards the end of this era, the first computer and transistor came into being, and began the contemporary era, thus creating a new, evolved model of high-technology within machining.
Today, machining is any of various processes in which a piece of raw material is cut into a desired final shape and sized by a controlled material removal process. Much of the modern day industrial machining process is carried out by computer numerical control (CNC), in which computers are used to control the movement and operation of the mills, lathes, and other cutting machines.

OUR MACHINING PROCESS
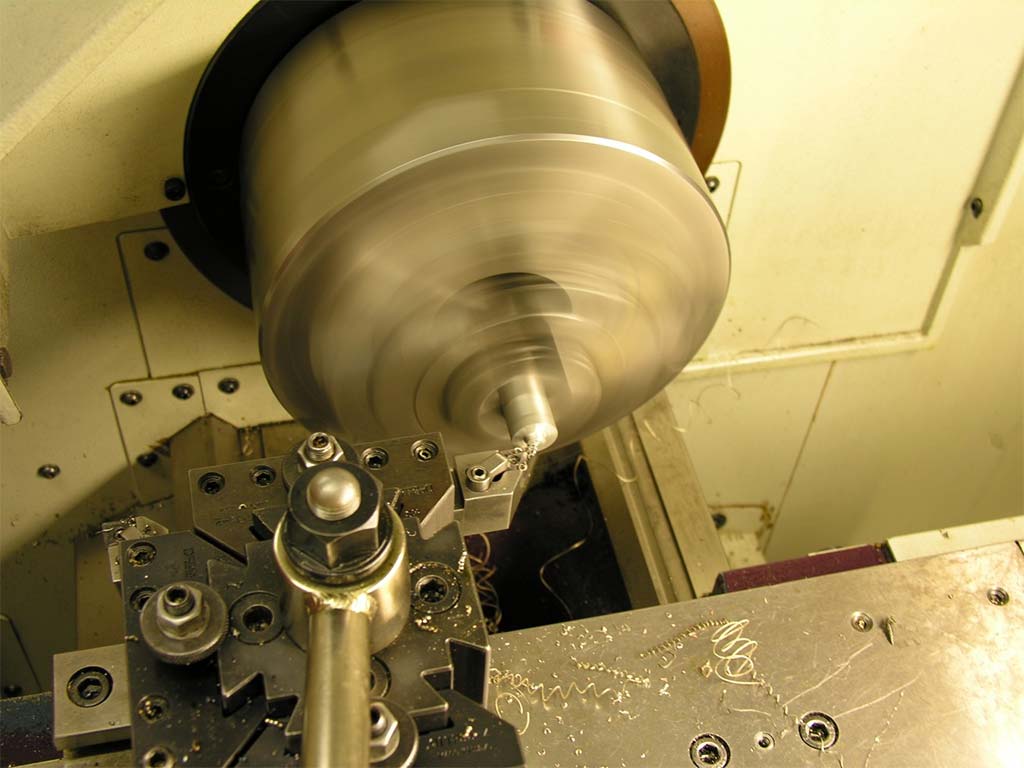

Drilling operations are done primarily in drill presses but sometimes on lathes or mills. Milling operations are those where the cutting tool rotates to bring cutting edges to bear against the work piece. Milling machines are the principal machine tool used in milling.
We have a variety of manual and CNC industrial machining equipment at Valley Forge & Bolt and take pride in having the expertise to use each and every one to satisfy our customers.
- Mazak QT-30 CNC Lathe
- Mazak QT-20 CNC Lathe
- Mazak “Nexus” QT250 CNC Lathe
- Mazak “Nexus” 100-II CNC Lathe
- Mazak “Nexus” QT350 CNC Lathe
- Mazak “Nexus” 450-IIM CNC Mill
- HAAS HS-1 HMC CNC Mill – 2 Pallet
- Other secondary manual machines include:
- Blanchard #18 Rotary Surface Grinder
- W&S #4 Turret Lathe
- Bardons & Oliver #6 Turret Lathe
- Fosdick 4 Spindle Drill Press
- Avey 3 Spindle Drill Press
- VIDEX 2″ Extrusion Machine