APPLICATION:
Split Case Compressor
LOCATION:
New York, USA
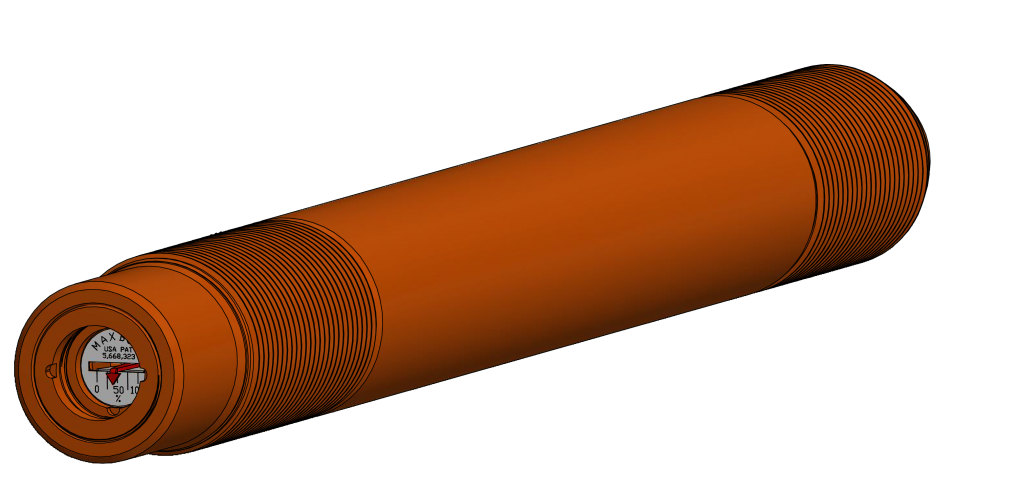
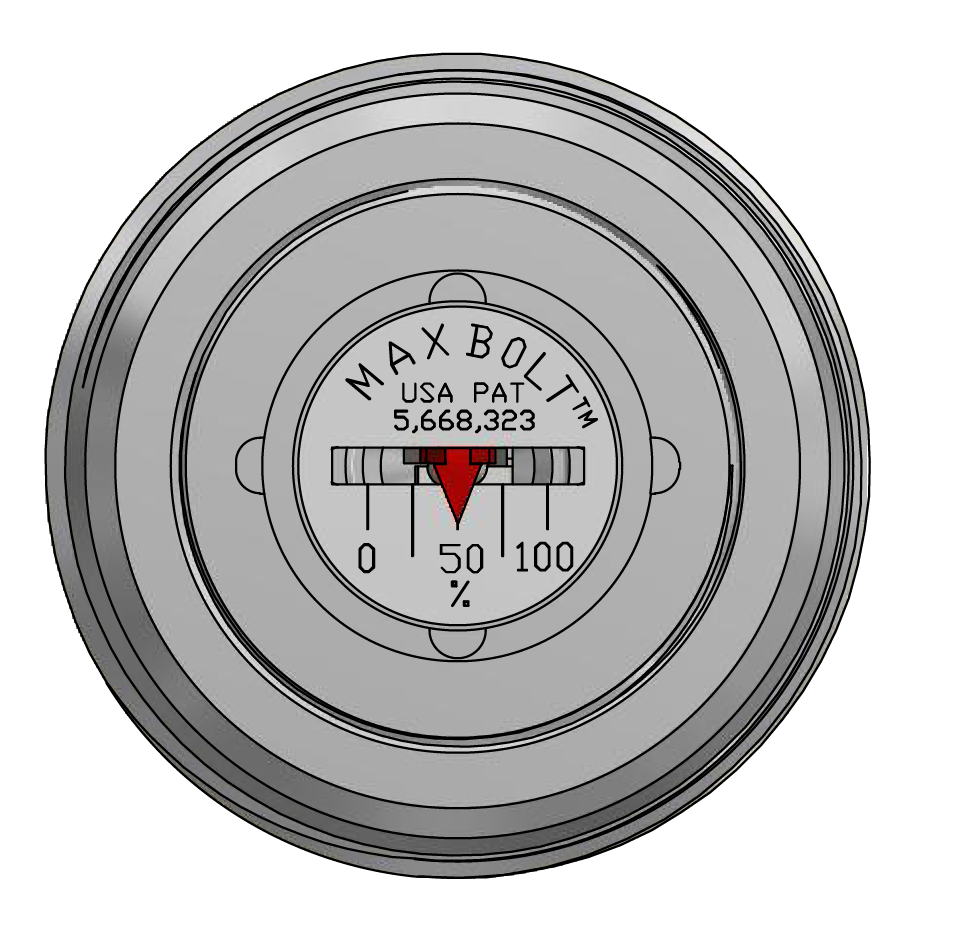
BOLTING ISSUE
This application is for case studs in a split case compressor. Bottom B of the case has studs threaded into it around the edge of the casting. Top A is lowered onto the case (and protruding studs), then nuts are used to tighten the studs.
In-between Bottom B of the centrifugal pump case and Top A is a gasket. It is imperative to have the proper load to compress the gasket and create a seal. Improper load on studs leads to improperly compressed gaskets and poor sealing on the split case pump.
SOLUTION
Maxbolt™ no-standoff load indicating studs were used in place of commodity class double ended studs.
INSTALLATION
Installation of the studs was faster with the ability to ensure proper load on the joint. By using the Maxbolt™ load indicating studs, the assembly team was ensured the proper load on the assembly and had zero failures when they conducted their hydro testing for leaks. Tightening was achieved by hydraulic wrench.
OUTCOME
This customer offers a split case compressor initially designed in the 1950’s. Every time they assembly this compressor it leaks when hydro tested. Every time. The last compressor they built using this design leaked 10 times on 10 different hydro tests. This caused a lengthy delay in manufacturing and many hours in assembly, disassembly and rework to achieve a properly functioning unit.
The first time the Maxbolt™ load indicating studs were used to assembly the compressor it had no leaks in hydro test.