APPLICATION:
38’ Sag Mill For Gold Ore
LOCATION:
CANADA
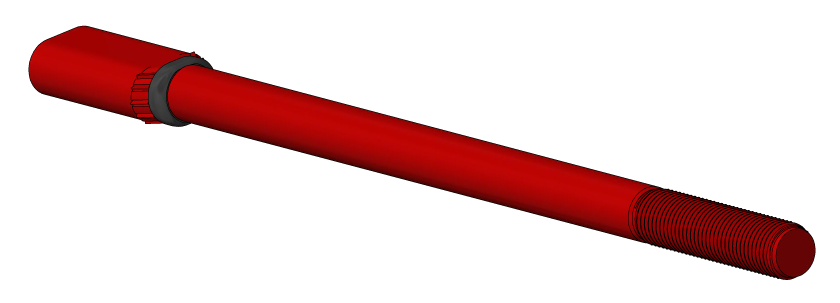
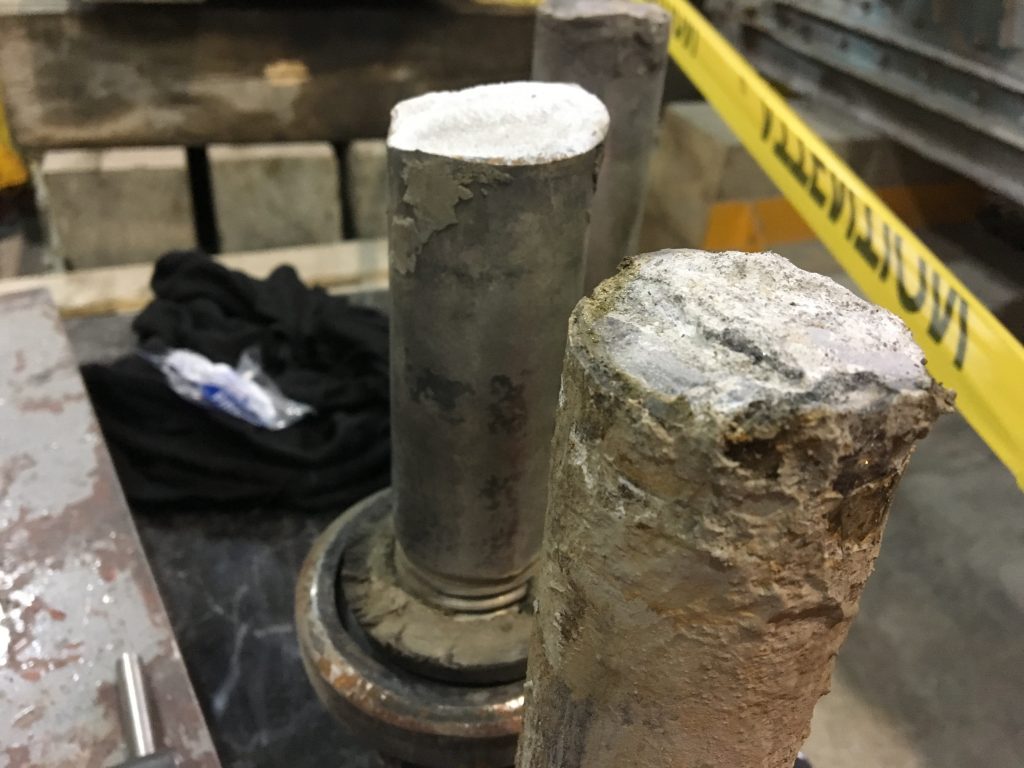
BOLTING ISSUE
Broken bolts on grate liners causing multiple unscheduled downs per month. Unscheduled down time cut into production numbers, lost time, and lost revenue.
SOLUTION
Valley Forge’s solution included two improvements:
Training on the usage of the Clarkster Tester unit for proper tool calibration for best installation results.
Replacing tradition liner bolt with the new Valley Forge Sealing Mill Ridgeback for improved performance.
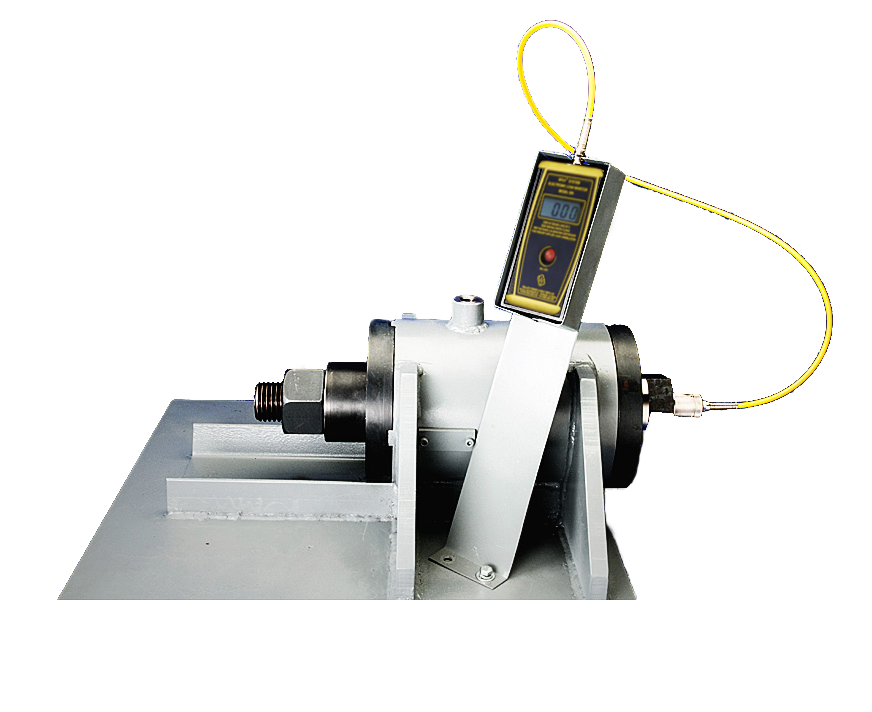
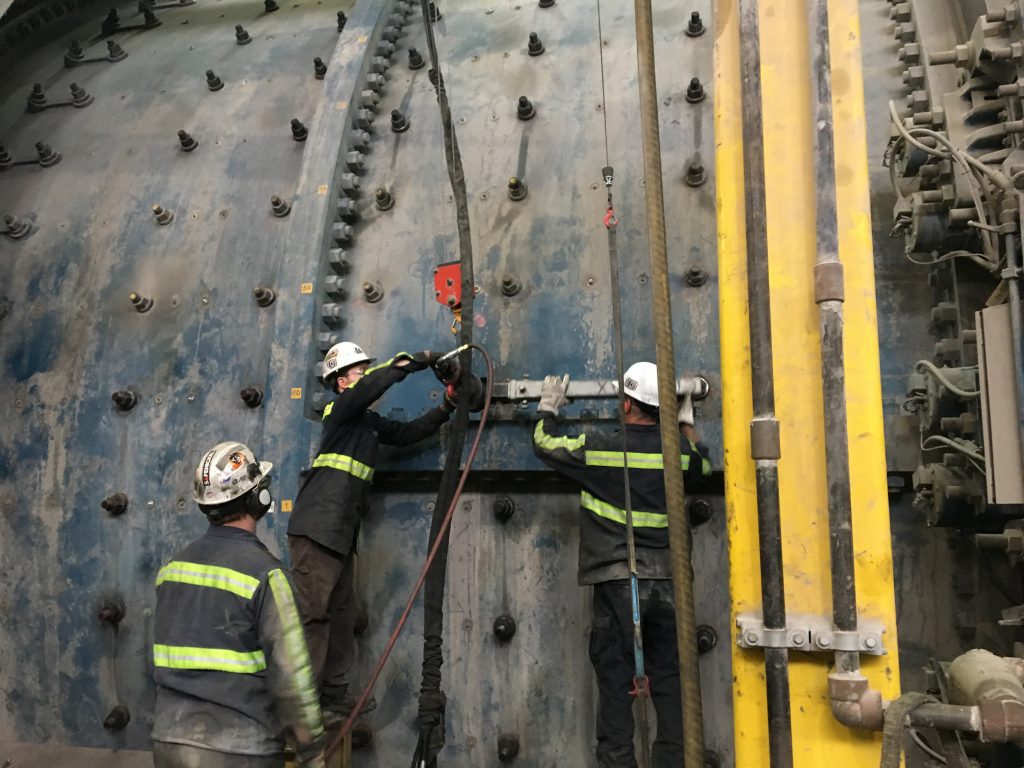
INSTALLATION
Installation took place under supervision of Valley Forge tech support. PT-9 torque multipliers where to be used for final tensioning, which were calibrated to required load using the Clarkster unit. The Clarkster Tester allows tools to be calibrated to the type of bolts being used allowing for a more accurate and consistent load throughout installation. The average load for previous installs checked by Valley Forge where only 72,000 lbf. This is 40,000 lbf less than minimum recommended for this application.
OUTCOME
Using the VF Sealing Mill Ridgebacks® and calibrated installation method has resulted in two consecutive runs with zero grate bolt breakage. Solving this bolting issue has eliminated costly unscheduled down time for bolt breakage.
Two hours of downtime for each broken bolt at a cost of $189,000 per hour in lost production.
WITH VF FASTENERS AND THE CLARKESTER:
Saved $3,000,000 in the first nine months.